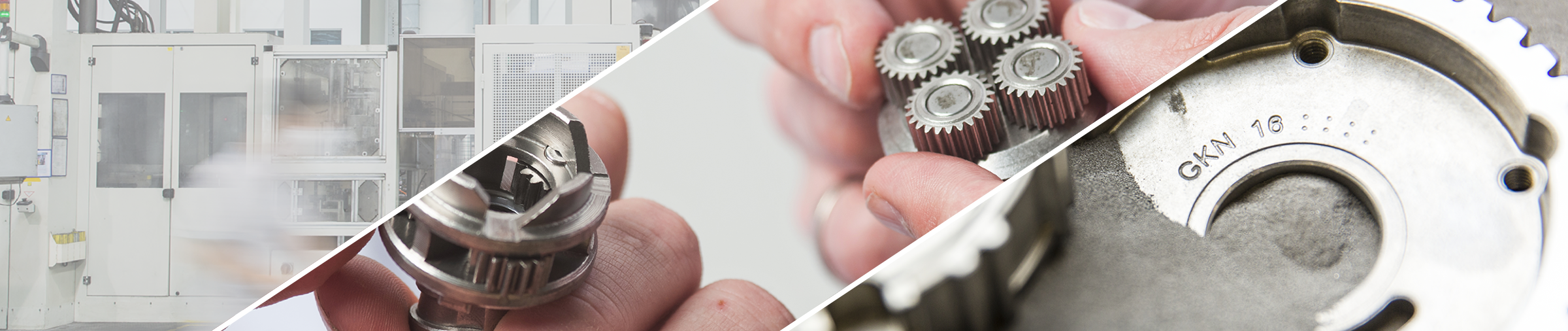
FLUIDIZING IN THE FOOD & BEVERAGE INDUSTRY
Fluidization is a process where solid particles are blown with gas, often through a porous metal media with sufficient force, to cause the particles to rise and move inside the container. The particles become mixed with one another and with the liquid or gas. Fluidized beds are used in industrial applications, as the process mixture provides a medium for transfer of heat or mass from gas to the solid particles and vice versa.
The onset of fluidization is when the upward flow of gas exerts more force than the downward force of gravity, which causes the solid particles to behave as a fluid. The particles begin to separate from one another and vibrate. If the gas velocity continues to increase, the particles will spread farther and move vigorously. High velocities will send the particles swirling in the container. Thus, fluidization can be fine-tuned to control the gas flowing through the porous metal - providing a range of bed conditions from laminar to turbulent flows.
The challenge
The particle size, shape and density of the solid particles will change the results of the fluidizing process. The product particle size must be bigger than the pores of the sintered metal. Also, the delta p of the fluidized bed media must be calculated according to customer product load to avoid common problems like “funneling, rat-holing or bridging” of the stored product.
The function
GKN Sinter Metals Filters offers tailor-made designed fluidizing equipment for new and existing systems. Available media of porous bronze, stainless steel and polyethylene offer optimal gas distribution - resulting in mass flow or mixing results. Fluidizing cones, made of sintered metal, are often self-supporting and delivered with required connecting flanges.
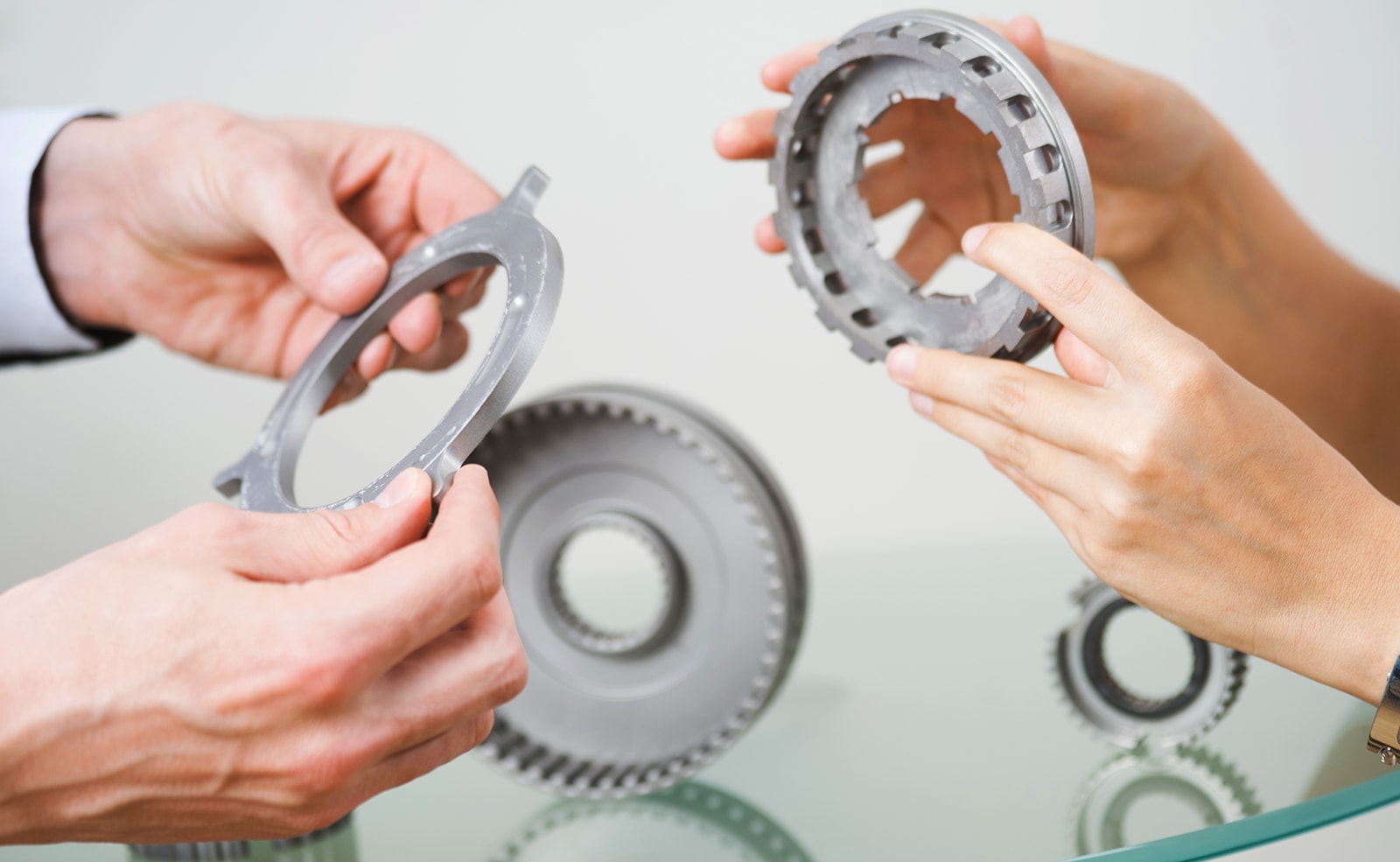
SPARGING AND GAS INTRODUCTION IN THE FOOD & BEVERAGE INDUSTRY
GKN sparging equipment and elements are used in applications where gas liquid contacting is required for reaction, stripping, mixing or diffusion purposes.
Our sparging elements are used for carbonation of soft drinks, edible oils Oxygen stripping, and others. In many applications, we help our customers to maximize process efficiency by recommending and designing the best suitable solution based on a variety of sparger units.
Advantages:
- Large variety of standard and custom sizes/shapes available
- Defined and homogeneous gas distribution
- Application and design support available
- Materials, mostly 316L SS and 304L SS, that comply with food industry standards
- Cleanable and reusable materials
- Sanitary surface finish available where required
The challenge
Stripping oxygen out of edible oils (vegetable oils).
Objective: Reduce costs by extending life cycle of oil
- Oxidation contributes to rancidity of edible oil
- Sparging with nitrogen reduces oxygen levels and minimizes oxidation
The function
Oxidation in oils reduces the product's shelf life. Traditionally, oxygen is stripped out of edible oils to protect them and increase shelf life. The old-fashioned process consisted nitrogen being pumped through 1mm drilled holes in pipes, acting as the sparger. Nitrogen bubbles were around 6mm in diameter. This was inefficient, as the larger the bubble, the more time and nitrogen was needed in the process. GKN porous metal sparger elements utilizing a 3 micron nominal pore size to create nitrogen bubbles around 50 to 100 microns. This increases the surface area of the gas in the product 40x (depending on the gas exit velocity). This process saves a significant amount of process time and 40-50 percent of Nitrogen gas usage.
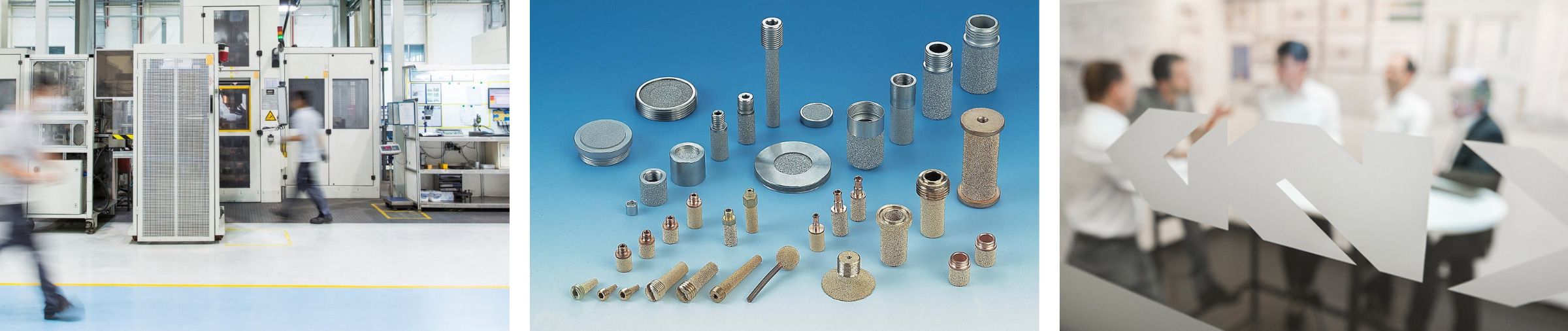
LIQUID FILTRATION IN THE CHEMICAL INDUSTRY
Many chemical reactions are initiated and aided by catalysts. These are often made of precious metals such as Palladium (Pd/C), Platinum (Pt/C), Rhodium (Rh/C), Ruthenium (Ru/C) etc. Typically five percent and ten percent palladium/platinum/rhodium/ruthenium on activated carbon/aluminum catalysts finds application in reactions like hydrogenation, reduction, oxidation etc. Since precious metal catalysts are expensive, their recovery is important from an economic and environmental point of view.
Often Raney Nickel is used as a versatile hydrogenation catalyst, which is widely used in laboratory and industrial hydrogenation processes. Some industries and products that take advantage of this process are:
- Food
- Aromatic
- Rubber additives
- Pesticide intermediates
- Fine organic chemical products
- Pharmaceuticals
- Petrochemicals
- Dyes & drugs intermediates
- Caprolactam
- Sorbitol
The challenge
While the catalyst is necessary, all particles have to be removed from the final product. During the catalyst's lifecycle, particles can be grinded off. A catalyst with a particle size of e.g. 25 micrometers (D50 value) can decrease significantly over time to e.g. 10 micrometers (D 50). To guarantee a stable flow or delta p in the process, a reliable and maintenance-free filter is required.
At the same time, the filter cake – expensive catalyst - must be recovered for reuse or refreshing.
The function
GKN Sinter Metals Filters offers customized self-supporting filter elements with filters up to 0.1µm as the finest filter grade in liquid. The patented metallic membrane, a dual sandwich design of two sinter connected powder grades, offers excellent cake release and improved flow compared to conventional designed filter. Designed metallic membrane SIKA-R AS for catalysts guarantee a perfect filtration and back pulse efficiency up to 0.1µm.
Due to the weld-free design with solid connection, our filter elements having a life cycle of 15 years based on application.
Get in touch
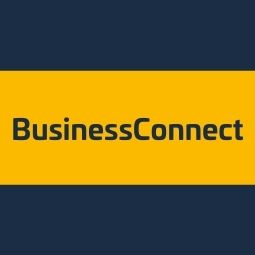